As seen in Sisma website : SWA, laser welding and mold maintenance system with fiber source.
SWA, laser welding and mold maintenance system with fiber source.
SISMA has decided to take an important step in the world of molds, presenting a new product to expand the current range, an absolute novelty and available on the market as early as May 2021.
SWA has been specially designed to perform modifications and repairs to molds damaged by wear or use.
The use of lasers, with the addition of materials, has revolutionized the traditional welding techniques of molds, allowing repairs without the need of preheating. This avoids the common collateral damage induced by traditional welding, such as geometric distortions, edge burns and decarburization.
Thanks to the properties of the laser beam, complex areas such as narrow and deep grooves, or internal and external edges, can be welded. The metallurgical quality of the weld meets the highest standards on all steels, copper alloys, and aluminum. The hardness of the welding layers can reach very high values without the need for subsequent heat treatments. Its simple way of operating and perfect visual inspection of the filler material, using a stereomicroscope, make this technology accessible to everyone, without having to rely on highly qualified technicians.
SWA is powered by a new generation laser source that offers greater energy efficiency and allows for high productivity.
Productivity
The new SWA introduces more process stability and a high-quality laser beam. These features increase the production rate, while consistently guaranteeing flawless process execution.
Maintenance-free
The new SWA does not have any consumable parts and is maintenance-free. The engineering team has pushed the boundaries of energy efficiency, making this the most efficient SWA ever made.
Advanced software functions (TRACKED ROUTES)
The processing parameters are managed through software that allows any operator to carry out advanced welding operations practically and intuitively. These software functions include welding along circular paths, on inclined planes, filling, and the overlap function for executing extremely regular weld seams.
FOCUS ON: software functionalities.
The features offered by SWA include the process optimizations that operate at a software level, developed to excellently accompany and assist in the welding execution. Both of these functions are part of the SWA package offered by SISMA which includes, in addition to the machine, the software dedicated to its operation.
PULSE SHAPING operates on laser welding by optimizing its qualitative and functional performance, specifically in two critical areas: the beginning and the end. During the welding pulse, PULSE SHAPING is able to modulate the power delivered by the laser beam in these two particular points, to avoid the arise of porosity, incisions on the edges or surface depressions that can be generated in the stream, ensuring a correct thermal cycle of heating, melting and cooling. This in addition to avoiding the challenges mentioned above, allows welding varieties of steel with a high content of carbon, materials sensitive to cracks and metals with different welding points.
SMART PULSE, on the other hand, manages welds that require very low laser power. Commonly fiber sources do not allow low values of power, therefore precision welding (using wires with a diameter of less than 0.3 mm) often shows over-penetration or incision defects at the edges. Thanks to SMART PULSE it is possible to control the power delivered even down to reduced values and will guarantee a deposit result without defects.
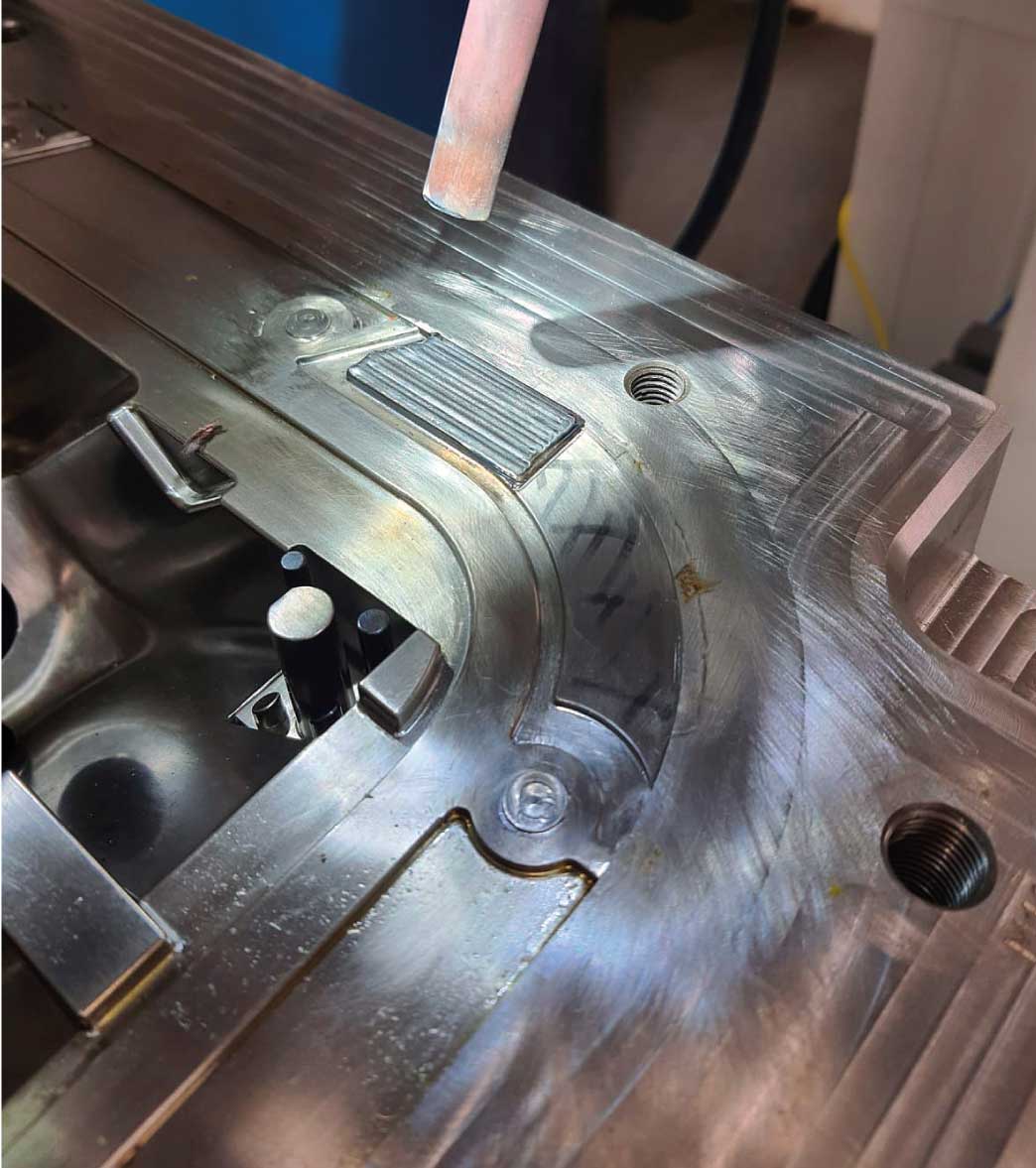
Rebuilding of a mold thanks to the “filling” function, obtained by exploiting the advanced “TRACKED ROUTES” software functions.
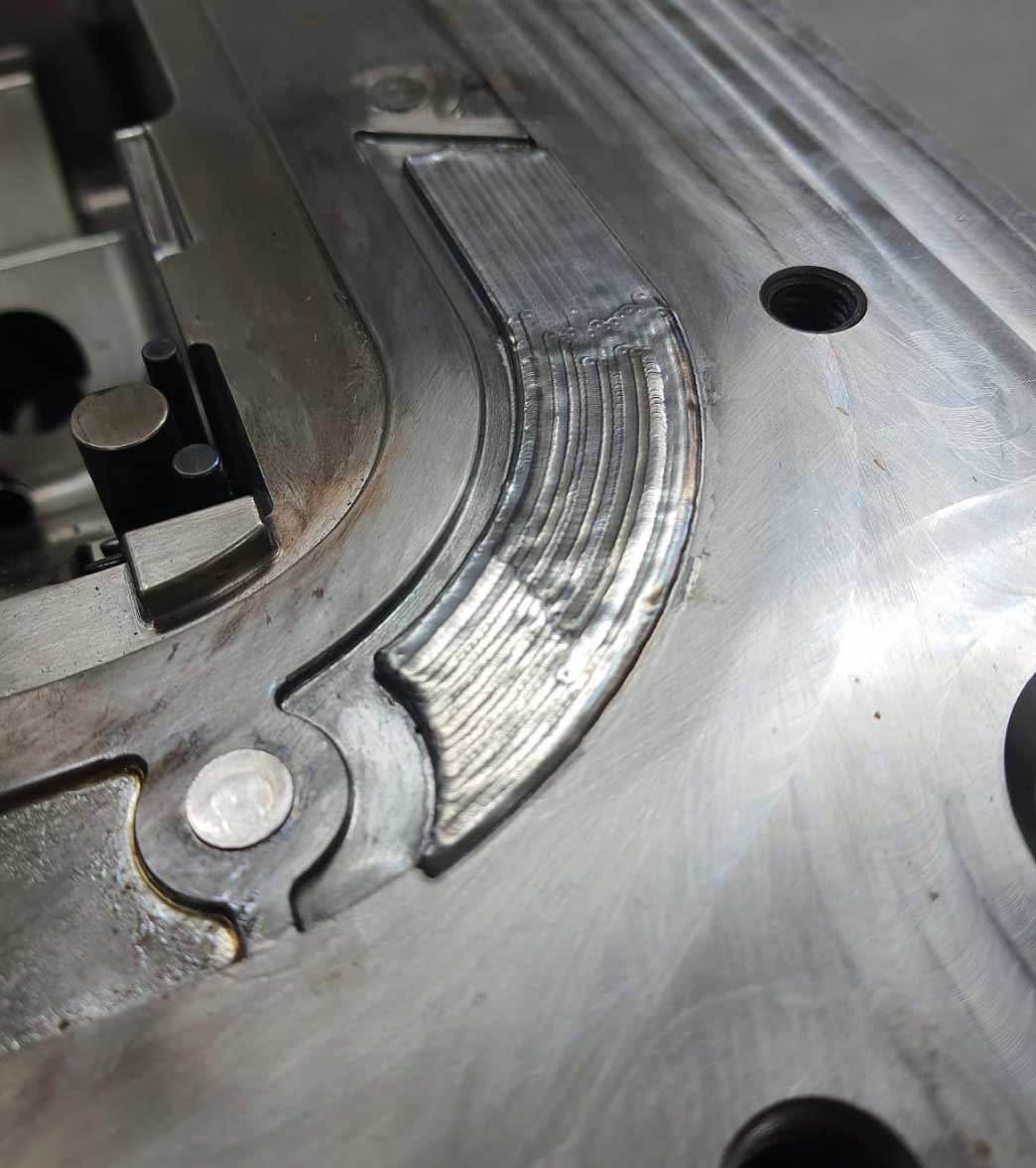
Rebuilding of a mold thanks to the “arc/circumference” function, obtained by exploiting the advanced “TRACKED ROUTES” software functions.
Industry 4.0, the future of manufacturing is today.
A large number of SISMA laser products are already part of the “Industry 4.0” paradigm, including SWA. These machines are capable of interconnection and integration through open and documented standard protocols, which are supported by modern production control systems and management systems. A turning point towards the future, Industry 4.0 technology helps manage and optimize every phase of the process, giving access to data and information in real time, and allowing to make decisions quickly and intelligently to increase efficiency and profitability.